rockwell hardness test disadvantages|rockwell hardness test explained : factories Advantages of Rockwell Hardness Test. Typically, the Rockwell test is easy to execute and more precise than other kinds of hardness evaluations. The Rockwell test technique is used on all metals, except when . WEBFailed to load picture. CorinnaKopfs. Corinna Kopf Newest OF Leaks MÈGA Folder August 31 Updated.. 🔥🔥 lînk in comments🔥🔥. Free. Auto. Click to watch more like this. Home. .
{plog:ftitle_list}
MyPSt - Seu ranking definitivo! Veja todos aqui 06/07/2023 15:49:26 XP Games : MENSAL SEMANAL 2635: 2706: 1414: 1374: 1224: 1163: 1489 : 207,900,901. 342 DeckardCain--sanctuary of chaos. alberto quer fazer o trofeu mais dificil se tornar ais facil? me adicione Postado em 6:12 p.m. Fevereiro 28, 2024 .
rockwell hardness testing chart
used industrial centrifuges
The Rockwell method has the following disadvantages: It is not always the most accurate hardness testing method, as even a small differential depth measurement error can lead to a significant error in the calculated hardness .Disadvantages of the Rockwell Hardness Test. 1. Limited Applicability to Soft Materials; 2. Surface Sensitivity; 3. Indentation Size Limitation; 4. Inability to Assess Microstructural Variations; 5. Scale Dependency; Rockwell Hardness .The Rockwell method has the following disadvantages: It is not always the most accurate hardness testing method, as even a slight error in measuring the depth difference can result in a significant error in the calculated hardness value. The Subtleties of Superficial Rockwell Hardness. Designed exclusively for thinner materials or specific surface layers, the Superficial Rockwell method operates with lighter loads. This reduced pressure results in .
Advantages of Rockwell Hardness Test. Typically, the Rockwell test is easy to execute and more precise than other kinds of hardness evaluations. The Rockwell test technique is used on all metals, except when .
What is Rockwell hardness testing? The Rockwell Hardness Test is generally a non-destructive test performed on samples when it’s necessary to determine how hard a material is. It’s generally considered easier to perform compared to .The disadvantages of Rockwell hardness test include the possibility of causing damage to the material surface during indentation, its limitation in testing very soft or very hard materials, and its inability to provide accurate results for . Steel Hardening Explained. Hardness Testing Conversion Table. The values below are estimated based on widely accepted conversion references such as ASTM E140, . Disadvantages: Applications: Load Range (kgf*) Indentation Type: Standards: Rockwell C (HRC) Metals, Alloys: Quick, easy to use, widely recognized: . The Rockwell hardness test involves applying a sequence of loads to the material and measuring the depth of the resulting indentation, which indicates the material’s hardness. .
The concept of the Rockwell Hardness test is essentially similar to its counterparts. A sample material is fed on to either a digital or manual Rockwell hardness tester which would then drop a set load ending with an .
Duration of Brinell and Rockwell Hardness; The Brinell test is very slow (30 – 60sec). Rockwell’s test is shorter (10 – 15sec). . Disadvantages of Brinell and Rockwell Hardness; Disadvantages of Brinell’s method are that hardness of ≥ 650 HB cannot be measured; the hardness is dependent on the load and according to X (degree of load .The Vickers Hardness test has some disadvantages also which are as follows: The good preparation (grinding and polishing) of the surface of the sample is important as quality matters, otherwise, it is hard to get a precise estimation of the object as intended is evaluated optically. . The speed of the method is not very efficient relative to . Rockwell hardness testing can determine the hardness of most metals, alloys and plastics, ranging from the softest bearing materials to the hardest steels. Photo: Wilson Instruments, An Instron Company. Stanley P. Rockwell invented the Rockwell hardness test. As a metallurgist for a large ball bearing company, he wanted a fast, nondestructive .
rockwell hardness tester diagram
Advantages and Disadvantages Of the Rockwell Hardness Test. The Rockwell hardness test is a widely adopted method for evaluating the hardness of materials, especially metals. It provides numerous advantages that have made it a preferred choice across various industries. However, it's crucial to acknowledge its limitations and potential drawbacks.The Rockwell hardness test is less affected by surface rough-ness compared to other methods such as the Vickers or Brinell tests. It can provide reliable hardness measurements even on surfaces with moderate roughness, making it a practical choice for a wide range of materials and surface conditions.Hardness test methods in the macro range include Brinell, Vickers and Rockwell. Hardness testing in the low-load range applies when the test load falls between an interval of 0.2 kgf and 5 kgf (test load ≥ 0.2 kgf and < 5 kgf). The most commonly used low-load method is Vickers. Low-load hardness testing is mainly used for testing of small .Rockwell hardness test measures the permanent depth of indentation on the material by applying a fixed load using an indenter. The smaller the indentation value, the harder is the material. The Rockwell hardness test follows the principle of the differential-depth method. Here, the indenter makes a residual depth called the indent and it is .
The Rockwell Hardness test is a widely used method to determine the hardness of metallic materials, thanks to its simplicity and quickness. This hardness test is based on indentation and depth of penetration, and it can be performed on various metals, including aluminum, copper alloys, brass, soft steels, and hard carbon steels. .
Scale C (carbide) testers are used for testing cemented carbides in the Rockwell A Scale, where tolerances of ± 0.20 of a Rockwell Hardness point are required. A specially selected “A” Brale penetrator is used to measure the hardness of cemented carbides in accordance with ASTM B 294 and the Cemented Carbide Producer’s Association (CCPA).A Rockwell hardness tester. The Rockwell scale is a hardness scale based on indentation hardness of a material. The Rockwell test measures the depth of penetration of an indenter under a large load (major load) compared to the penetration made by a preload (minor load). [1] There are different scales, denoted by a single letter, that use different loads or indenters.
The Vickers hardness test is ideal for testing of all metals and is therefore the method with the widest range of application. The hardness test method according to Vickers is described in standards ISO 6507 (Metallic materials – Vickers hardness test – Part 1: Test method) and ASTM E384 (Standard Test Method for Microindentation Hardness (1gf - 200 gf) of Materials .Applications of Rockwell Hardness Test. Quality Control: Commonly applied in industries that require hard materials on parts and other manufactured products. Material Selection: This tool supports the process of identifying materials that will be applicable depending on the hardness needed. Heat Treatment Evaluation: Using the assessment of the hardness of the treated .While the Rockwell hardness test has its uniqueness, its accuracy is also guided by some critical factors you need to consider before engaging in this test method. Rockwell Testing Machine – The machine itself is one critical consideration for an accurate Rockwell test result. And though the Rockwell test is often seen as very easy and quick .The Leeb method is a quick and portable hardness test method, which is determined by the ratio of rebound velocity to the impact velocity of a moving impact body. It is best applied to solid parts of the object for example casting and forgings. In the article, we include the advantages and disadvantages of Leeb method in details.
The Rockwell hardness test method is a simple process that uses a diamond cone with a round tip for harder materials and a hardened steel ball indenter for softer ones. With every test, two loads are applied to the test subject. First, an .Two common hardness tests are used in the industry: the Rockwell scale and the Vickers scale. Both test the surface of a material, but they are used for different purposes. The Rockwell hardness test measures the hardness of all metals except in conditions where the structure of the test sample would cause too much variations, or the indentations formed would be too .
Denoted by NDT(Non-Destructive Testing) It is a technique to inspect and test a sample without any damage so that it can be used for the further process if found OK. The first machine used to test steel bearing races. Rockwell hardness test experiment The Rockwell hardness test is, A technique used to calculate the hardness of a material.Hardness is the property of a material that enables it to resist plastic deformation, usually by penetration. However, the term hardness may also refer to resistance to bending, scratching, abrasion or cutting. Hardness testing is a crucial aspect of metallurgy, as it provides valuable insights into a material’s mechanical properties and overall quality. There are various methods available for measuring hardness, each with its own set of advantages and limitations. In this blog, we’ll delve into the Vickers Hardness Test and discuss when it’s best to use this method over other .profiles. The Rockwell test is the most popular indentation hardness test and is used in a wide variety of applications. Advantages of the Rockwell Test There are several reasons for the popularity of the Rockwell test. The test itself is very rapid. On a manually operated unit, a Rockwell test takes only five to ten seconds,
Therefore, hardness values can only be compared if they have been obtained by identical test procedures. The most important procedures and their advantages and disadvantages are explained in more detail below: Brinell hardness test (explained in this article) Vickers hardness test; Rockwell hardness test What are the disadvantages of Brinell hardness test? The Brinell test leaves a relatively large impression on the surface, which can be a disadvantage for some applications. It’s also slower compared to Rockwell testing. . HRC (Rockwell C) is a specific hardness scale within the Rockwell hardness testing method.In today’s article, we will be learning an important hardness test and its name is the Rockwell hardness test. It is quite different from other prominent hardness tests like Brinell and Vickers hardness test.This test gives you the direct reading of the hardness of .The Rockwell hardness test method, as properly defined in ASTM E-18 standards, is the most commonly used hardness test method among all the other methods. + 86 755 61301520 [email protected]
The Knoop method has the following disadvantages. The surface quality of the specimen must be good, because the indent is measured optically. . (compared with the Rockwell method). The test cycle takes somewhere between 30 and 60 seconds, not including the time taken to prepare the specimen. Due to the need to conduct optical indent .
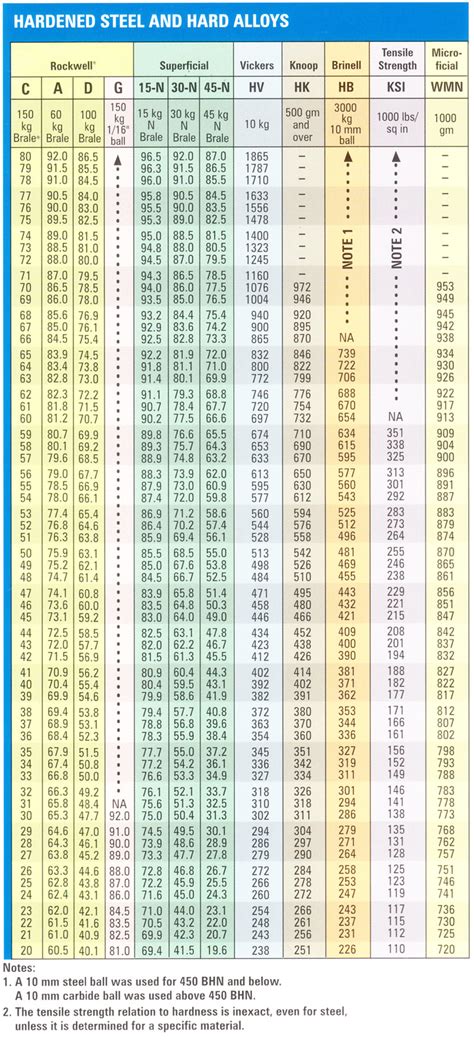
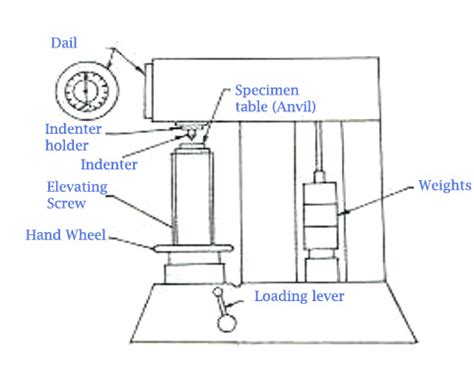
WEB126- Combo Chicken (Apenas delivery) De R$ 34,00 por R$ 25,50. Arroz Chop suey, 4 Hot sushi, Cubos de filé de frango empanado, acompanhados de molho tarê e gergelim, 2 .
rockwell hardness test disadvantages|rockwell hardness test explained